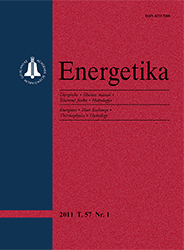 ISSN 0235-7208
|
2010 m. Nr. 2
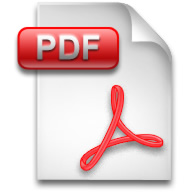 Realization and analysis of inorganic metal oxide plasma melting and fibrillation process
Mindaugas MILIEŠKA, Romualdas KĖŽELIS, Vitas VALINČIUS, Vladas MĖČIUS
The proposed new plasma technology for the production of fiber from inorganic metal oxides overtakes traditional sustaining technologies due to the simplicity of processing and a good quality of the obtained product. The paper contains a description of a uniflow plasma chemical reactor designed for melting and fibrillation of ceramic materials, an analysis of its optimal exploitation conditions at atmospheric pressure and a characterization of the final product obtained during realization of the plasma fibrillation process. Air was used as the plasma-forming gas and propane-butane as the additional supporting gas. The power of the plasma torch was in the range 65–69 kW. Mineral fiber was manufactured from different dolomite and quartz sand mixtures. Dolomite content in the mixtures varied from 25% to 35%, as the purpose of the experiment was to elucidate the influence of dolomite content in the mixtures on the quality of the obtained mineral fiber. The temperature and velocity of gas leaving the reactor was 2 316–2 516 K and 500–530 m/s, respectively. Then a mixture of 60% of quartz sand and 40% of dolomite was used with two different designs of the plasma chemical reactor to determine the influence of the velocity of flow leaving the reactor on the quality of the obtained mineral fiber. The temperature of the flow was 2 900–2 970 K, and its velocity increased from 794 m/s to 1 759 m/s. The structure and morphology of mineral fiber were examined by scanning electron microscopy (SEM). The process of fiber formation was analyzed by visualization using a CCD camera. Fibers have been formed by kinetic energy of the flow. The mechanism of fiber formation is explained. Mineral fiber produced employing the plasma fibrillation process is resistant to high temperatures (up to 1 300 °C); the diameter of the fiber filament doesn’t exceed 2–5 μm. It is more suitable for the production of high temperature or noise isolators, catalysts or filters.
Keywords: plasma, plasma-chemical reactor, mineral fiber
|
Numeriai:
2011 - T.57 Nr.1, Nr.2, Nr.3, Nr.42010 - T.56 Nr.1, Nr.2, Nr.3-42009 - T.55 Nr.1, Nr.2, Nr.3, Nr.42008 - T.54 Nr.1, Nr.2, Nr.3, Nr.42007 - T.53 Nr.1, Nr.2, Nr.3, Nr.42006 Nr.1, Nr.2, Nr.3, Nr.42005 Nr.1, Nr.2, Nr.3, Nr.42004 Nr.1, Nr.2, Nr.3, Nr.42003 Nr.1, Nr.2, Nr.3, Nr.42002 Nr.1, Nr.2, Nr.3, Nr.42001 Nr.1, Nr.2, Nr.3, Nr.4 |